News
Weezle Diving goes green
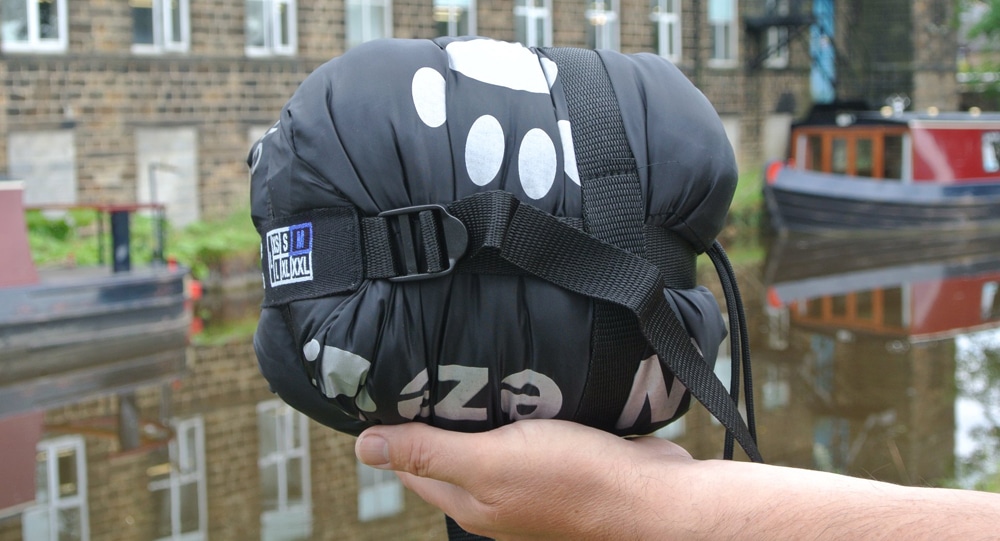
When Weezle Diving (www.weezle.co.uk) launched their first product in 1998 it was green. Literally. A bright emerald one-piece ‘Extreme’ undersuit. What was equally innovative was the packaging the Weezle Extreme came in. It was green too. This time, environmentally green. The Extreme undersuit was packed in a lightweight durable material sack, that could be compressed to save on space.
The fact that Weezle set out to be as environmentally friendly as possible from day one was no happy accident. In LBW (life before Weezle), Paul Child – Weezle’s co-founder – worked in the packaging industry, and as such was exposed to some interesting ideas that influenced his ecological thinking.
The compression sack set a trend and Weezle introduced draw-string fabric bags for their long boots and unbleached cotton duffle bags for bigger products. They switched out plastic barbs and replaced them with small metal safety pins to secure cardboard product tags to their Russian Hats and base layers. “Although this solution is more labour intensive, we knew it was the right thing to do”, stated Paul Child.
Weezle also “did the right thing” when it came to sourcing the insulating material for their undersuits. “Thanks to the likes of the Women’s Institute and their plastic soup campaign the public are now learning about the environmental impact of microplastic fibres” stated Paul Child. “Our man-made filling has longevity and unlike Fleece this hydrophobic material does not break down into microfibres. It can also be successfully washed in cold water.”
All these small steps have helped Weezle Diving adopt the ‘Green Achiever’ scheme and achieve their aim of being 100% single-use-plastic free. This system works to improve day-to-day company operations. All aspects of the company are holistically evaluated. Typical audit questions include “do you have an environmental policy? Do you know your carbon footprint? Where do your drains go? How do you dispose of plastic, wooden pallets, oil rags and fluorescent light bulbs? Do you take back old and redundant products from your customers? What forms of energy to you use (electricity, gas oil, renewable?) Does your company car fleet use biofuels? Do you source supplies locally?
“We reviewed our ancillary despatch materials because this is one area that everyone routinely overlooks”, stated Paul Child. “This year we have been sourcing packaging that can be composted. Bubble wrap is not an option, the obvious solution is corrugated cardboard. But what about the ‘documents enclosed pouch’? Traditional pouches used by the likes of UPS, Fedex etc are made from plastic and the backing paper that is removed to stick the pouch to the package can’t be always recycled either. After much searching we have sourced a pouch manufactured from oxo-biodegradable polythene. We have also switched out our packing tape for a compostable one that uses a water-based glue and all our cardboard boxes have already been previously used. In addition we have reached and agreement with our suppliers that if they dispatch us something that we cannot reuse or recycle, they have agreed we can return it to them for disposal.
Being awarded this Green Achiever certificate has been a real pat on the back! We have now joined Mission 2020 and will continue to use biodegradable, compostable packing materials, and recycle and reduce our ecological footprint where possible.”
For more information please visit the Weezle Diving website by clicking here.
News
Dive Worldwide Announces Bite-Back as its Charity of the Year
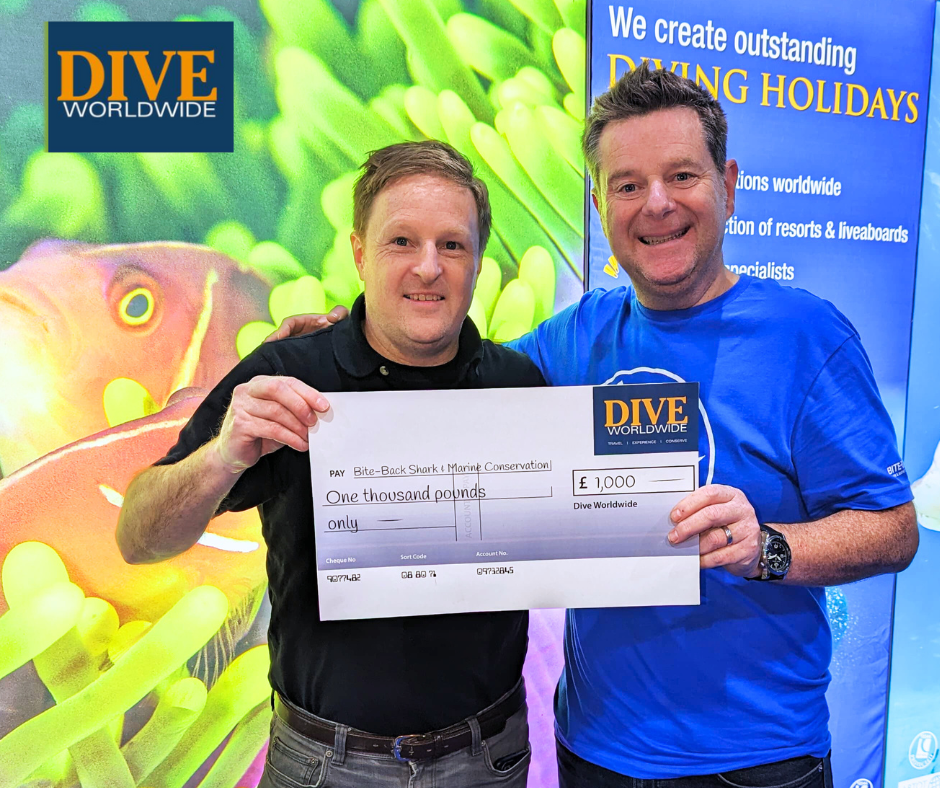
Over the next 12 months, specialist scuba holiday company Dive Worldwide will be supporting Bite-Back Shark & Marine Conservation with donations collected from client bookings to any one of its stunning dive destinations around the world. The independently-owned operator expects to raise £3000 for the UK charity.
Manager at Dive Worldwide, Phil North, said: “We’re especially excited to work with Bite-Back and support its intelligent, creative and results-driven campaigns to end the UK trade in shark products and prompt a change in attitudes to the ocean’s most maligned inhabitant.”
Bite-Back is running campaigns to hold the media to account on the way it reports shark news along with a brand new nationwide education programme. Last year the charity was credited for spearheading a UK ban on the import and export of shark fins.
Campaign director at Bite-Back, Graham Buckingham, said: “We’re enormously grateful to Dive Worldwide for choosing to support Bite-Back. The company’s commitment to conservation helps set it apart from other tour operators and we’re certain its clients admire and respect that policy. For us, the affiliation is huge and helps us look to the future with confidence we can deliver against key conservation programmes.”
To launch the fundraising initiative, Phil North presented Graham Buckingham with a cheque for £1,000.
Visit Dive Worldwide to discover its diverse range of international scuba adventures and visit Bite-Back to learn more about the charity’s campaigns.
MORE INFORMATION
Call Graham Buckingham on 07810 454 266 or email graham@bite-back.com
Gear News
Scubapro Free Octopus Promotion 2024
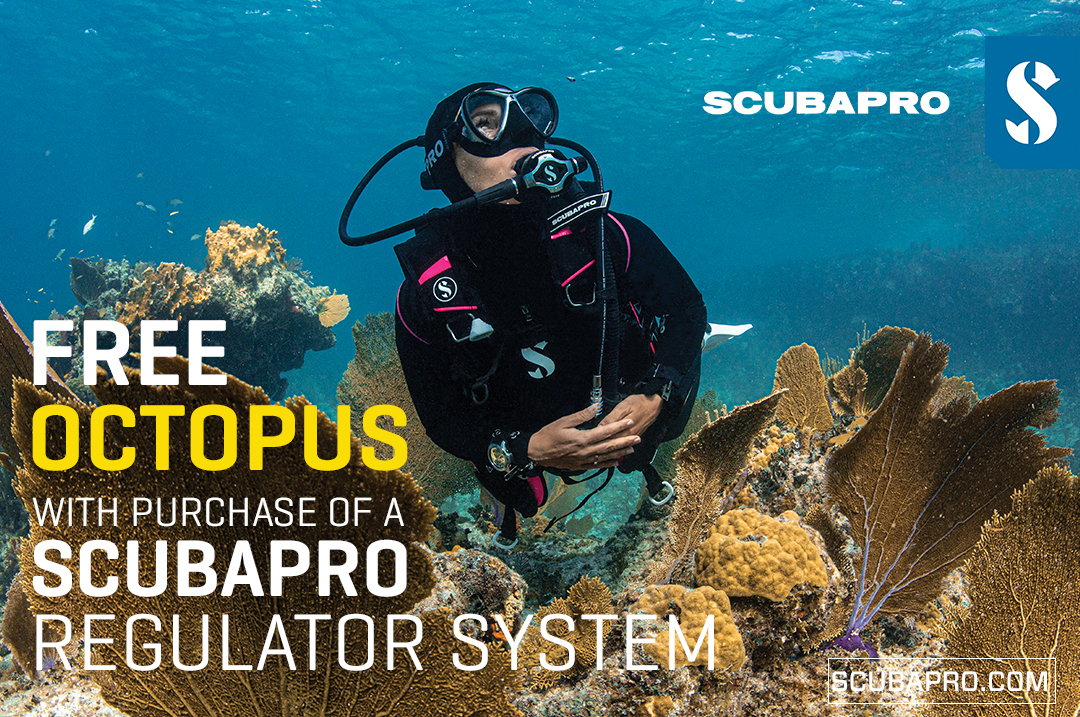
Free Octopus with every purchase of a SCUBAPRO regulator system
Just in time for the spring season, divers can save money with the FREE OCTOPUS SPRING PROMOTION! Until July 31st SCUBAPRO offers an Octopus for free
with every purchase of a regulator system!
Get a free S270 OCTOPUS with purchase of these combinations:
MK25 EVO or MK19 EVO with A700
MK25 EVO or MK19 EVO with S620Ti
MK25 EVO or MK19 EVO with D420
MK25 EVO Din mit S620Ti-X
Get a free R105 OCTOPUS with purchase of the following combinations:
MK25 EVO or MK19 EVO with G260
MK25 EVO or MK17 EVO with S600
SCUBAPRO offers a 30-year first owner warranty on all regulators, with a revision period of two years or 100 dives. All SCUBAPRO regulators are of course certified according to the new European test standard EN250-2014.
Available at participating SCUBAPRO dealers. Promotion may not be available in all regions. Find an authorized SCUBAPRO Dealer at scubapro.com.
More information available on www.scubapro.com.
-
News3 months ago
Hone your underwater photography skills with Alphamarine Photography at Red Sea Diving Safari in March
-
News3 months ago
Capturing Critters in Lembeh Underwater Photography Workshop 2024: Event Roundup
-
Marine Life & Conservation Blogs3 months ago
Creature Feature: Swell Sharks
-
Blogs2 months ago
Murex Resorts: Passport to Paradise!
-
Blogs2 months ago
Diver Discovering Whale Skeletons Beneath Ice Judged World’s Best Underwater Photograph
-
Gear Reviews2 weeks ago
GEAR REVIEW – Revolutionising Diving Comfort: The Sharkskin T2 Chillproof Suit
-
Marine Life & Conservation2 months ago
Save the Manatee Club launches brand new webcams at Silver Springs State Park, Florida
-
Gear Reviews3 months ago
Gear Review: Oceanic+ Dive Housing for iPhone